【課題解決】ブロー成形の後工程の効率化で生産性が向上
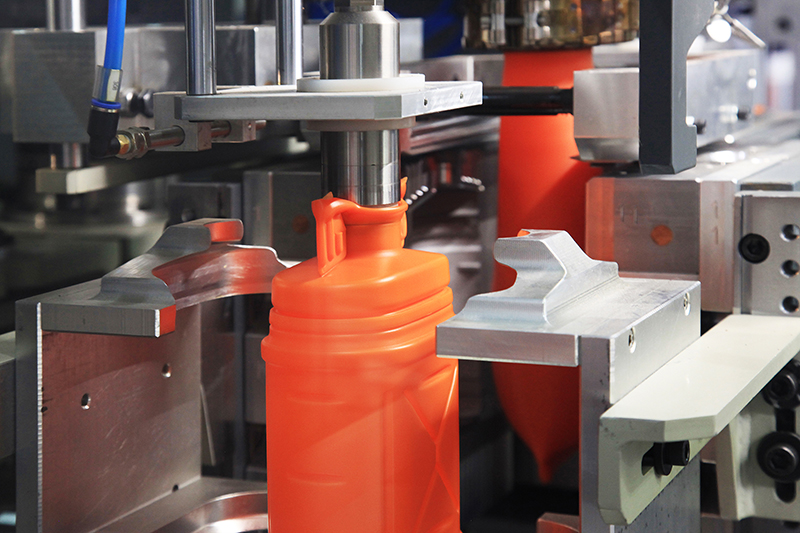
プラスチック製品の大量生産に欠かせない樹脂成形。なかでも中空構造の形状をつくりだす「ブロー成形」は、ペットボトルをはじめ、自動車用ダクトやオイルタンク・パイプなどさまざまな筒状製品の製造で用いられています。
この記事では樹脂成形工場における、ブロー成形の後工程のお困りごとをご紹介します。
ブロー成形後の穴あけ工程の課題
合わせ目が無く機密性の高いブロー成形。射出成形にくらべ大型製品を低コストで成形することができますが、そこで課題となっているのが、ブロー成形後の「穴あけ」加工です。
ブロー成形は原理上、加熱したペレット(樹脂)に空気を注入して膨らませるため、あらかじめ穴の空いた形状を成形することができません。そのためブロー成形後の穴(取付け穴やスリットなど)は、ルーターによる手作業やプレス加工によってあけられています。
しかし1メートルを超えるような大型の成形品の場合、移動や段取りひとつとっても大変で、作業効率が上がらないことも… 手作業による穴位置精度のバラつきも問題となっていました。
現場では「段取りを増やしたくない」「決まった位置に正確に穴をあけたい」などの声があり、穴あけの作業効率をいかに上げるかが課題となっていました。
POINT課題のポイント
- ブロー成形後の穴あけ加工を効率化したい
- 手作業による穴位置精度のバラつきで困っている
ブロー成形後の穴あけを「エアーニッパーパンチブレード」で解決
従来ブロー成形後の穴あけは手作業で行われることが多く、効率化や自動化の妨げとなっていました。特殊な金型を使うこともありますが、コストがかかるため少量多品種の生産現場では現実的ではありません…
そこで採用されているのが「エアーニッパーパンチブレード」です。
エアーニッパーパンチブレードは、お客様ごとの専用設計。「丸穴」「長穴」「スリット」など、穴や切れ込みの形状に合わせた専用パンチで、ブロー成形後の穴あけ加工を効率よく行うことができます。
また片刃が固定されているため位置決めがしやすく、精度の高い穴あけが可能。圧縮エアを使うため加圧力が高く、ルーター作業にくらべ削りカスも出ないためクリーンな作業が可能です。
10台のエアーニッパーパンチブレードを自動機に組み込み、1日の生産数が100個から1000個にまで大幅に上がった事例もあり、ロボットハンドへの取り付けで、さらなる自動化も実現します。
(パンチブレード別作品は、弊社営業部へお問い合わせください)
効率的なブロー成形後の穴あけ加工で、現場の生産性向上におこたえします。
POINT解決のポイント
- ブロー成形後の穴あけ加工の効率化で、生産性向上が実現
- エアーニッパーパンチブレードで、精度の高い穴あけが可能
関連商品
お問い合わせフォーム
本記事についてのお問い合わせは、下記のフォームからご連絡ください。
課題解決事例は課題解決のための皆様の「気付き」となればと考えています。更なる改善案などがございましたら是非とも共有させていただきたいと存じます。
掲載に関しては都度、ご確認の上追加掲載させていただきます。