【課題解決】小ロット・試作の基板リードカットの負担を軽減
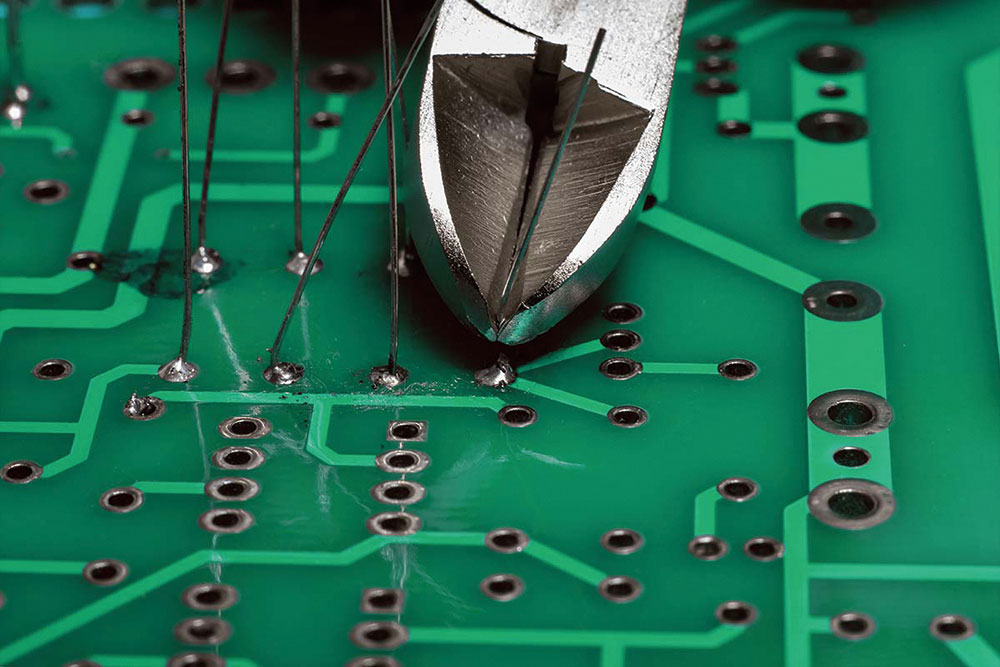
電子機器の開発サイクルの短縮が進むなか、電子部品製造の現場では、小ロットのプリント基板や試作基板のニーズがさらに高まっています。こうした基板は、現在も手作業によるはんだ付けが欠かせません。しかし現場では、手作業にともなう負担や品質不良が課題となっていました。
この記事では、小ロット・試作の基板におけるリードカットのお困りごとをご紹介します。
基板製造におけるリードカットの課題
小ロットのプリント基板や試作基板の実装は、自動化が難しく、DIP部品のはんだ付けからリードカットまで、現在も手作業に頼る工程が多くあります。特に、抵抗・ダイオード・コンデンサなどのリード付き部品を実装した後、余分なリード線をハンドニッパーで一本ずつ切断する作業(リードカット)は、基板1枚あたりの処理数が多く、作業者にとっても大きな負担となっていました。
このような作業では、繰り返しカットすることで手首を痛めやすく、力の入れ方によっては、カット後の出代にばらつきがでてしまうことがあります。また、リード線のカット片が基板に接触し、傷つけてしまうことも…
現場からは、「作業負担を軽減したい」「品質を安定させたい」といった声が上がっていました。
POINT課題のポイント
- ハンドニッパーによるカットが負担
- リード線の出代を一定にしたい
- 基板の傷を防ぎたい
リードカットの課題を「エアーニッパー」で解決
リード線のカット後の出代は、+2.5mm(クラス2)や+1.5mm(クラス3)など、IPC規格(電子機器の組み立てにおける品質評価基準)によって規定されています。さらに一部のメーカーでは、実装条件に合わせて、IPC以上に厳しい社内基準を設けている場合もあり、リードカットには高い精度が求められます。
そこで採用されているのが、「レバー式エアーニッパー」です。
レバー式エアーニッパーは、手持ちで使用する手動式のエアーニッパーです。本体をホールドし、レバーを握ることでブレードが作動。ハンドニッパーと比べて疲れにくいため、連続カットの負担が軽減し、カットの品質が安定します。
ベッセルでは、リードカット専用のバキューム機構付きの別作仕様をご用意しています。カットと同時に、不要なリード線を回収することで、基板にカット片が接触して傷がつく心配もありません。
リード線の出代の長さについても、ブレードの特注で対応することが可能です。お客様の仕様に合わせて、最適な別作エアーニッパーをご提案します。
POINT解決のポイント
- 連続カットの負担を軽減
- リード線のばらつきがなくなる
- 基板の傷つきを防止
関連商品
お問い合わせフォーム
本記事についてのお問い合わせは、下記のフォームからご連絡ください。
課題解決事例は課題解決のための皆様の「気付き」となればと考えています。更なる改善案などがございましたら是非とも共有させていただきたいと存じます。
掲載に関しては都度、ご確認の上追加掲載させていただきます。