【解決解決】容器搬送時の静電気除去でホコリの混入を防止
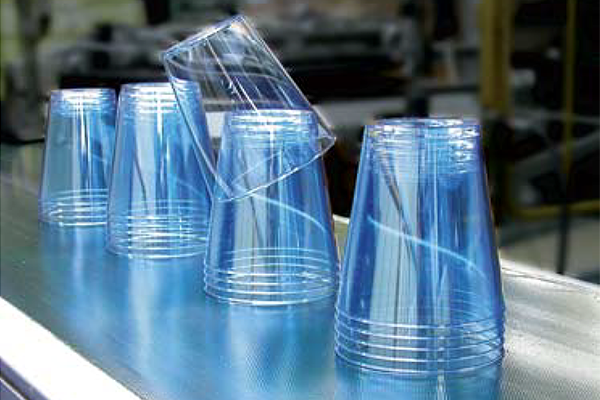
食品業界にとって重要な異物混入対策。異物の原因は、機械から出る金属片や作業者の毛髪などさまざまです。なかでも対策が難しいのが「容器」へのホコリの混入です。
この記事では樹脂成形工場における、プラスチック容器の搬送工程のお困りごとをご紹介します。
容器搬送時の静電気によるホコリの課題
従来、射出成形機で製造された食品カップやトレーなどの「プラスチック容器」は、取り出し機からベルトコンベアやストッカーに移され包装工程へと搬送されます。
この時、容器に帯電した静電気が原因で容器どうしが反発してしまい、スタッキング(積み重ね)不良になることがありました。スタッキングが正しくできていないと、静電気によって容器の内側にホコリやチリを引き寄せてしまい、食品への異物混入の原因となってしまいます。
現場ではいかに容器に帯電した静電気を取り除き、搬送時の「スタッキング不良」や「ホコリの付着」を防ぐかが課題となっていました。
POINT課題のポイント
- スタッキング不良やホコリの付着で困っている
- 作業者による監視や、不良による廃棄をなくしたい
容器搬送時のホコリの付着を「静電気除去ファン」で解決
静電気の原因は、金型と樹脂が擦れあうことで発生する「摩擦帯電」と、成形品を取り外す際に発生する「剥離帯電」です。スタッキング不良は、特に軽いプラスチック容器で起こりやすく、同じ極性(プラスとマイナス)の静電気が容器に蓄積することで発生します。
そこで採用されているのが「静電気除去ファン」です。
静電気除去ファン〈F-6RST/F-120R/F-120S/CF-300/L-90〉は、ファン型のイオナイザー。コンベア上からイオン化されたエアーを送風することで、容器に帯びた静電気を除電しスタッキング不良を防止します。
静電気除去ファンは、ピンポイントで除電する「ノズル型」と異なり、広範囲にイオンを拡散させることができるため、工場のコンベアの広い範囲で除電が可能。スタッキング不良の防止は、製品のカウントエラーや自動化ラインでの包装不良の改善にもつながります。
容器搬送時のホコリの付着防止で、現場の生産性向上におこたえします。
POINT解決のポイント
- 静電気除去ファンによる除電で、スタッキング不良を防止
- ホコリの付着をなくし、生産性向上が実現
関連商品
お問い合わせフォーム
本記事についてのお問い合わせは、下記のフォームからご連絡ください。
課題解決事例は課題解決のための皆様の「気付き」となればと考えています。更なる改善案などがございましたら是非とも共有させていただきたいと存じます。
掲載に関しては都度、ご確認の上追加掲載させていただきます。