【課題解決】インサートフィルムの静電除去で二枚取りを防止
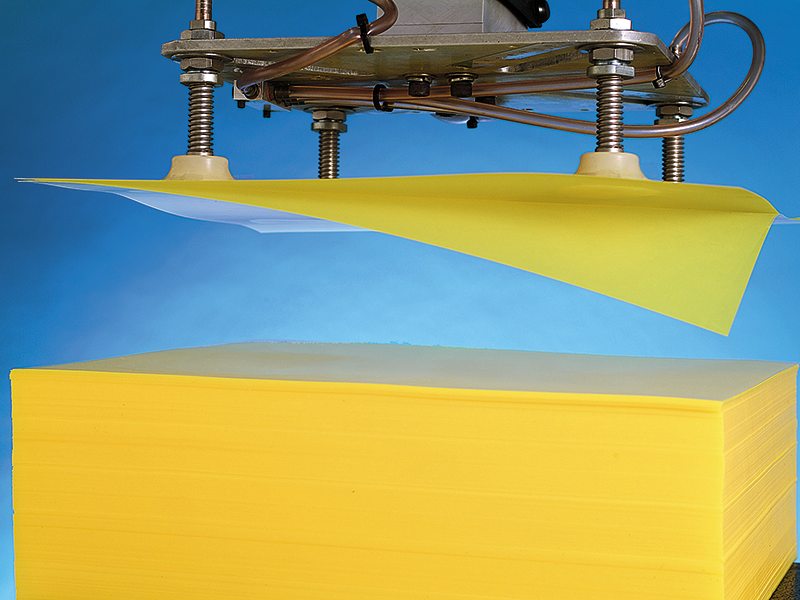
デザイン性が求められる樹脂部品に欠かせないフィルムインサート成形。フィルムインサート成形は、印刷されたフィルムを金型内部に挿入し、樹脂部品の表面に貼り付ける一体成形技術です。自由なデザイン性と優れた耐久性で、自動車内装パネルや家電部品で多く使われています。
この記事ではフィルムインサート成形における、フィルム搬送時のお困りごとをご紹介します。
フィルムインサート成形のフィルム搬送工程での課題
近年フィルムインサート成形の需要が増える中、課題となっているのがインサートフィルムの搬送工程でのトラブルです。
従来積み重なったインサートフィルムを射出成形機に送る際、搬送装置を使いフィルムを一枚ずつピックアップし金型内部に挿入します。しかしフィルム厚さが数ミクロンと薄く、静電気によって密着してしまい二枚取りしてしまうことがありました。
そのまま次の工程に進んでしまうと、搬送エラーによるライン停止や不良品発生の原因となります。
微弱なエアを送りフィルムどうしの貼り付きを防ぐこともありますが、フィルムの材質や表面のコートによっては静電気でぴたっと密着してしまい、うまく剥がすことができません。
現場では後工程でのトラブルを防ぐために、いかにフィルムの密着を防ぎ二枚取りによる誤送をなくすかが課題となっていました。
POINT課題のポイント
- ・フィルムの二枚取りによる誤送で困っている
- ・フィルムの隙間に発生した静電気を除去したい
- ・搬送エラーによるライン停止や不良品発生をなくしたい
フィルムの帯電を「ノズル型イオナイザー」で解決
樹脂製のインサートフィルムは絶縁体のため、移動中の振動や擦れによって静電気が蓄積されてしまいます。またフィルムをピックアップする際にも「剥離帯電」による静電気が発生します。
そこで採用されているのが「ノズル型イオナイザー」です。
ノズル型イオナイザー「静電気除去ピンポイントノズル〈N-3〉」は、スポット除電に最適なノズル型のイオナイザー。搬送装置でピックアップしたフィルムの隙間にイオン化されたエアを吹き込むことで、フィルムに発生した静電気を除電し二枚取りを防止します。
フィルムの隙間に発生した静電気は、表面から取り除くことができないため、パルス(間欠)エアを使いフィルムを震わせるとより効果的です。
狭いスペースでは、フィルムの高さに合わせたスリム型のバー型イオナイザー「静電気除去ハイパワーバー 〈HPBシリーズ〉」もおすすめです。
インサートフィルムの確実な除電で、現場の不良品削減におこたえします。
POINT解決のポイント
- ・フィルムの隙間に発生した静電気を除去し、二枚取りを防止
- ・搬送エラーによるライン停止や不良品発生を防止
関連商品
お問い合わせフォーム
本記事についてのお問い合わせは、下記のフォームからご連絡ください。
課題解決事例は課題解決のための皆様の「気付き」となればと考えています。更なる改善案などがございましたら是非とも共有させていただきたいと存じます。
掲載に関しては都度、ご確認の上追加掲載させていただきます。